Megaroller Opens Perth Office
- Australian Bulk Handling Review
- Oct 1, 2014
- 6 min read
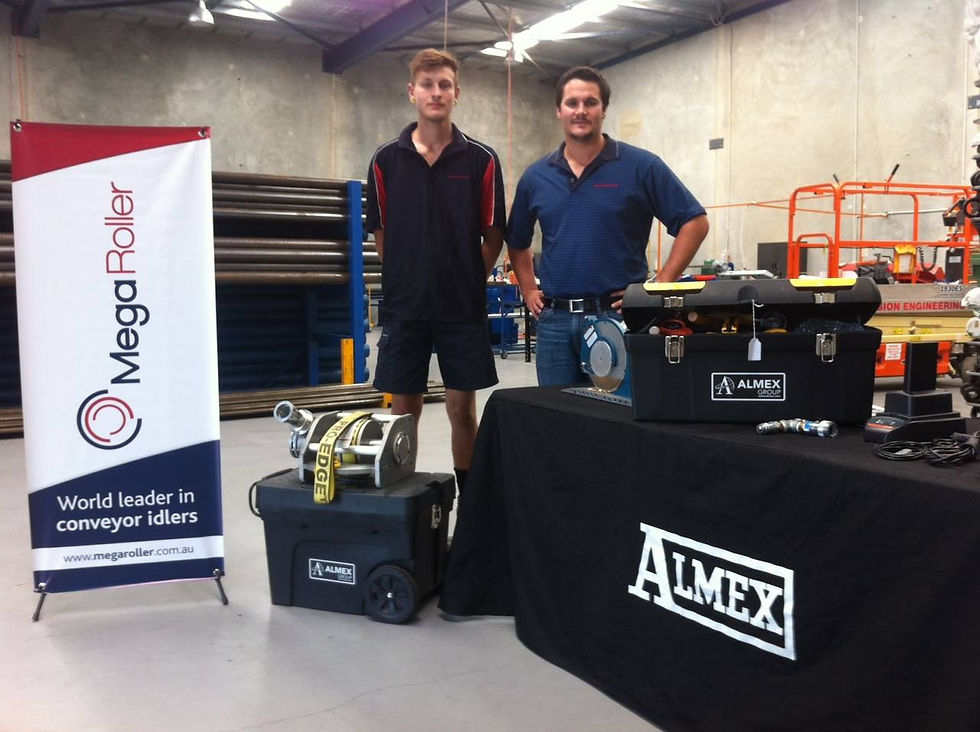
South African conveyor roller business Megaroller has sold its Australian arm to investor Jannie Kotze, who has opened a new office for the company in Perth, WA. Kotze spoke with ABHR’s Oliver Probert.
Megaroller has operated a factory in Morisset, NSW for the past half-decade, but the South Africa-based operators of the roller business were not particularly proactive in establishing the company as a major brand in Australia, Kotze explained to ABHR.
“What happened in Australia is because it was not the focus, they manufactured and distributed it here for the last five years, but not in a high-profile way,” he said.
Instead, Megaroller chose to be a bit more low-key, doing about half of its business directly with customers, and the other half through a range of distributors. “We’ve been in the Australian market for quite some time, but not in the high-profile, driven way.”
Kotze aims to change that.
“The [Megaroller] owner in South Africa asked me, because of my business background, to take charge of this one, and take it as an opportunity,” he explained. “So I looked at it, and re-looked at it, and in the end I decided it’s a good opportunity, and a good market. I think I’ve got enough energy, and so it’s an investment for me to take on and to grow.”
After buying Megaroller’s Australian business, Kotze set up an office for the company in June. He said the company is planning on opening a new factory in Perth, but it’s not yet clear how that would impact operations at the existing NSW premises.
Stephan Botha is the general manager of that premises, and he told ABHR the company’s real advantage comes from the quality of its high-density polyethylene (HDPE) rollers. The rollers, which he said are fire retardant but not FRAS rated, are for that reason best suited to hard rock conveying scenarios, but not underground coal conveyors.
“As a standard, we like to believe we can do double the life of a steel roller,” Botha said. “And if you have a look at the other polymer rollers in the market we would like to think we can outlast others in the industry three-to-four times over, just due to construction.”
While Botha conceded that roller life is highly based on the individual variables in each case, he’s confident Megaroller’s products will stand up well against any of their competitors.
“You have different environmental areas, different belt speeds, different weights on your belt,” he said. “So that all influences the lifespan of the roller … [but] what makes our roller different to the others is the construction we have. It’s a 14 to 16mm HDPE polymer sleeve, which is the external of the roller. Then it’s reinforced on the inside; normally the polymer roller manufacturers just have the polymer sleeve … they don’t have the reinforcement on the inside. Ours does have that reinforcement. That’s one of the key features when you look at a polymer roller.
“The other thing is the structure where your bearing housing and the roller face join. Mainly, the polymer manufacturers have just a press, so they press the bearing housing inside the tube, and that’s how they leave it. Under heavy loads, you’ll find that those two separate and give way – they fail – and that gives free access to dirt, water, dust and everything that can get to your bearings and ruin your roller. We actually fuse the bearing housing and the polymer sleeve together.”
That fusing process includes a lot of heat and pressure, but Botha explained that the company can fully construct the rollers at its NSW warehouse.
“That’s just one of our processes, to fuse the end housing (or the bearing housing) and the outer sleeve together … We’ve got three guys working here full time, on about 12 different stations.”
Employing three people, Botha said, current capacity at the NSW site is about 900 - 1000 rollers a month. Lifting that capacity, though, is as simple as adding staff.
“If you changed that to one person per machine, you’d be able to bump that up to roughly 3000 per month,” Botha said.
“We normally have a lead time of about 14 days for orders of up to 300 rollers,” he continued. “That quick turnaround time is good for miners because we’ve got quick delivery. It also means we don’t have big [order] quantities all at once. That’s one of the advantages of manufacturing locally.”
That turnaround also helps deal with Australia’s industries specifically, according to Botha.
“The Australian mining industry doesn’t have a standard when it comes to conveyor belts. South Africa has a standard, so for all the different belt widths, your frame slot sizes are set, and standard, so you can actually produce en masse. That’s where China comes in and plays its role well.
“In Australia, because we don’t have those standards, specifically with frame sizes, means [the Chinese builders] can’t have that quick turnaround of a standard product. That’s one of the other advantages of manufacturing locally, is we are pretty much a phone call away from getting the correct dimensions, and delivering the product within two weeks, or 20 days if it’s a big order.”
Turnaround time and unique order arrangements are some of the benefits Botha said Megaroller can offer its customers, and the company needs to be able to claim such advantages over competitors because its rollers are about 15% more costly than competing brands, Botha estimated.
“I think our product is about 15% more expensive than alternatives, but if you pay for our product, and your belts are clean (your scrapers are working), maintained and checked properly, we’ll give you a two-year warranty. So that 15% more actually buys you a little bit of peace of mind.”
Botha admitted that it is difficult to convince a minesite to pay a little bit more for its rollers, and it can be hard to convince an operator that rollers are anything but a commodity item.
“Rollers don’t have to be a commodity product, but it’s definitely hard to convert people’s thinking about conveyor rollers,” he said. “But this product will save you a lot of money in the long run. We’ve found that if you actually let someone try the product, they’ll find that they like the product. Not only does it last longer, it’s light weight, easier to handle, and is quiet.”
At times Botha has been told the rollers are too quiet, in fact. While most of the time a silent roller usually means it has failed, Botha said with Megaroller’s products, it’s often the other way around. “You install them, and it’s quiet. But when there’s noise then there’s an issue, that’s just the way of their design.”
Botha said Megaroller’s product is designed to overcome the most common problems found in everyday conventional conveyor use.
“Number one is that it’s belt friendly,” he explained. “The belt in itself is the most expensive part of the conveyor, and so you want to protect that section as much as possible. Having a product that damages that belt, for me, doesn’t make sense. That’s the reason we went with polymer, and polymer ends. A steel roller, with steel ends, should that bearing fail, you end up getting that knife cutting affect felt in the length of the belt. Once that’s done you can’t fix that.
“That’s where the real savings come in. If you’ve got a product that – even if it fails – won’t cut that belt in its length, it just makes sense to use that product.
“Number two is that it’s environmentally resistant. When you’ve got harsh environmental conditions like chemicals, the sea breeze, and the hot sun beating down, that’s all stuff that steel doesn’t like. If rust occurs on a roller then you’ve again got that possibility of damaging the belt. Polymer can resist those environmental factors. The structure of ours and that polymer makes it environmentally resistant.
“We machine the product off after the fusing has all been done. We machine the roller off, making it concentric, which also brings noise pollution down, stops the vibration, and balances it. All of that creates a better bearing environment. The heart of the roller is the bearing, and by doing all of those things, we can protect the bearing a lot better.”
Also related to the rollers’ bearings, Botha said, is his third key benefit: “Number three is our sealing arrangement. 99% of the market makes use of a labyrinth type seal, which if you inspect closely always has a free way for dust and moisture to make its way through to the bearing.
“We’ve actually introduced a patented sealing arrangement, where we put a polymer push on the shaft, where any contamination will need to creep underneath the polymer push – almost 70mm long. The amount of time contamination takes to get between the polymer push and the shaft is measured in years.”

Contact: www.megaroller.com.au
Comments